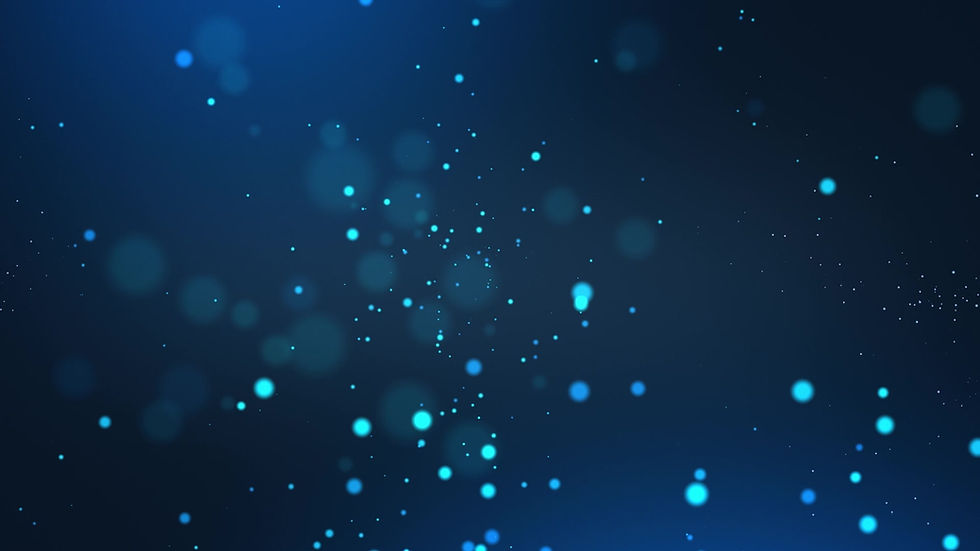
Operations &
Productivity
Your Challenges
Our Tools
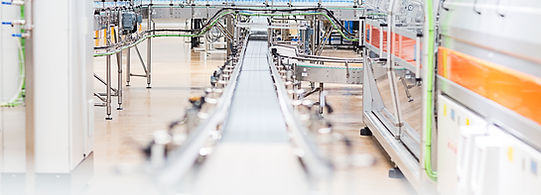
TrueNord’s experience with a large number of manufacturing businesses reveals that the productivity gap between the top & average performers can be as high as 30%. The gap varies by industry, but productive operations maintain low product cost and high product availability performance than others. High performers invariably make higher profits per unit, and they better fulfill customer expectations. Therefore, highly productive operations support two fundamental objectives of any business;
​
· Making more money
· Making customers happy
While operational productivity & excellence bring fundamental benefits, potential benefits are easier to articulate than ideal execution strategy. Most organisations fail with their operational productivity & excellence initiatives due to poor execution, they intend to do the right things but fail by doing things incorrectly. Impact of failure can be as detrimental as diminishing employee engagement and loss of trust to senior leadership.
Successful initiatives combine OpEx know-know with a thorough behavioral change plan and project management capability. Whether it is achieving higher equipment utilization with OEE improvements, or reaching high-quality levels and labour effectiveness or reducing defects with increased first-pass yield, reducing inventory, or increasing up-time by productive maintenance, organisations must prioritise potentials and adopt a proven execution strategy.
TrueNord has provided many client organisations with breakthrough productivity and performance improvements. Besides technical know-how, our consultants possess experience and skills on behavioural change. Please contact us to learn more about how we could help you stratify and successfully execute your operational productivity and excellence initiative.
....
-
Faster Unit Cost Increase Relative to Volume
-
High Throughput Time
-
High WIP (Work in Progress) Inventory
-
High FG (Finished Goods) Inventory
-
Process Optimisation
-
Multiple Process Bottlenecks
-
High Absenteeism
-
Low Compliance to HSE (Health, Safety & Environment) Standards & Requirements
-
Low Customer Satisfaction
-
Low Delivery Performance
-
Low Output per Employee
-
Low Product Availability
-
High Scrap Levels
-
Production Stoppages and Disruptions
-
Frequent Machine Break-Downs
-
Material Shortage, Missing Parts in Production
-
High Production Lead-time
-
High Cost of Production
-
High Frequency/Severe Accidents
-
Capacity & Investment Planning
-
Lay-out Planning
-
Poor Workplace Ergonomics
-
Insufficient Space to Match Production Footprint Requirements
-
Inefficient Operations
-
Low OEE (Overall Equipment Effectiveness) levels
-
Poor Quality Performance
Our proven tools, together with our knowledge and expertise in execution will help overcome operational issues and low productivty.
Shopfloor Management
5S &
Visual Factory
One Piece Flow
Levelling & Sequencing
Quick Change Over-SMED
TPM
Lean Management
Kanban &
Milkrun
Layout
Optimisation
Method & Line Balancing
RCA & Problem Solving
Six Sigma
Management PDCA
Business Process Re-engineering
RACI
Span of Control
Back to Services